Bugatti testuje pierwsze zaciski hamulcowe z tytanu wydrukowane na drukarce 3D
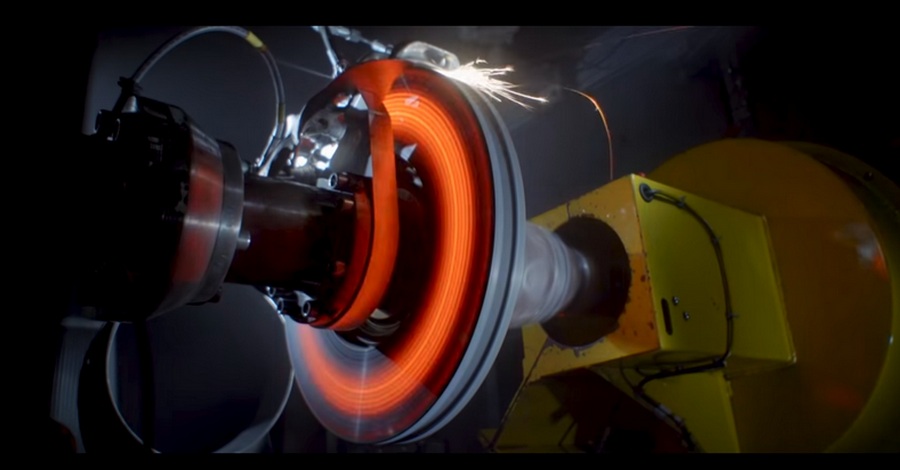
Komponent wyprodukowany w Hamburgu mierzy 41 cm długości, 21 cm szerokości i 13,6 cm wysokości. Wyprodukowany na drukarce 3D zacisk waży zaledwie 2,9 kg, czyli o całe 2 kg mniej od części obecnie stosowanej do produkcji Bugatti Chirona. Co więcej, nowe zaciski Bugatti zniosą obciążenie 125 kilogramów na każdy milimetr kwadratowy! Do produkcji tytanowego prefabrykatu użyto czterech 400-watowych laserów wchodzących w skład drukarki SLM 500 3D. Urządzenie pracowało przez całe 45 godzin, tworząc zacisk hamulcowy składający się z 2213 warstw tytanu. Przed wdrożeniem technologii na masową skalę proces, a w szczególności czas realizacji ulegnie optymalizacji.
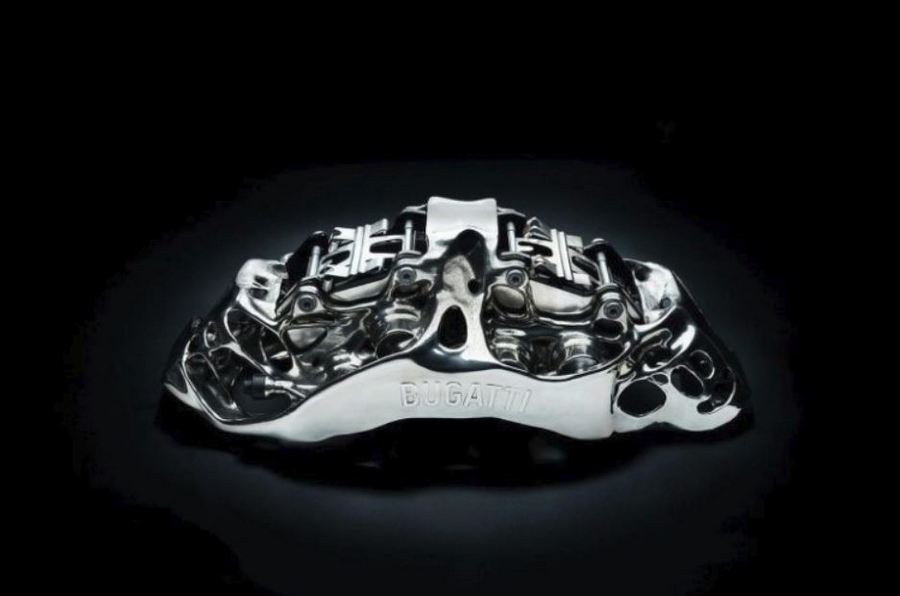
Rok później francuski producent samochodów należący do niemieckiej grupy z Wolfsburga zaprezentował swój koncept podczas testów określających jego wytrzymałość.
W sieci opublikowano oficjalny film przedstawiający tytanowy komponent w akcji.
Symulacja hamowania odbyła się przy maksymalnej prędkości prawie 400 km/h. Ciepło wygenerowane pod wpływem tarcia spowodowało nagrzanie samej tarczy do przeszło 1000 stopni Celsjusza! W takich warunkach doskonale sprawdza się tytan, który bardzo dobre odprowadza ciepło. To materiał idealny do zapewnienia akceptowanych warunków pracy przy hamowaniu z prędkości maksymalnej Chirona czy przyszłego Divo (pisaliśmy o tym tutaj). Wygląda więc na to, że przyszłość jest właśnie w druku 3D!
Tekst: Piotr Myśków